研削ディスクは、様々な産業において材料の成形や仕上げを容易にする上で重要な役割を果たしています。しかし、他の工具と同様に、効率や性能を低下させる問題から逃れることはできません。この記事では、研削ディスクによくある問題を詳しく解説し、その根本原因を探り、シームレスなワークフローを実現するための効果的な解決策をご紹介します。
導入
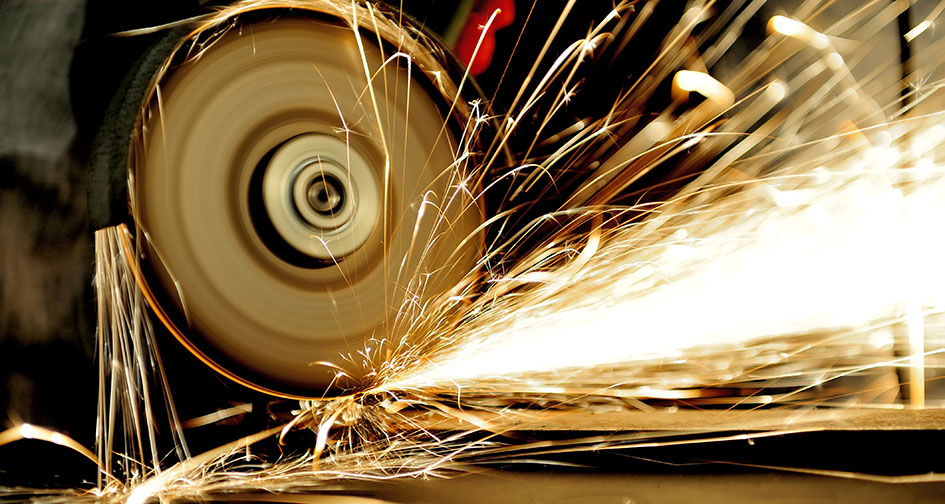
研削ディスクは、材料の除去、成形、仕上げ工程に不可欠なツールとして、様々な産業において重要な役割を果たしています。その定義、各産業における重要性、そして共通の課題を理解することは、研削ディスクの最適な使用方法と効率的な運用を実現するために不可欠です。
A. 研削ディスクの定義
研削ディスクは、機械加工工程において材料の表面を切断、研削、研磨するために使用される研磨工具です。これらのディスクは通常、研磨粒子を基材に接着したもので、余分な材料を除去したり、表面を滑らかにしたり、刃先を研いだりする回転工具を形成します。様々な形状とサイズがあり、それぞれ特定の用途に合わせて設計されています。
B. 様々な産業における重要性
金属加工産業:
金属加工・製造において、研削ディスクは金属表面の成形、バリ取り、仕上げに不可欠です。正確な寸法と表面品質を実現するために、アングルグラインダーと組み合わせて使用されることが一般的です。
建設業界:
建設専門家は、コンクリートの表面処理、粗いエッジの平滑化、石やコンクリートなどの材料の欠陥の除去などの作業に研磨ディスクを使用しています。
自動車産業:
研削ディスクは、自動車業界において、工具の研磨から金属部品の成形・仕上げに至るまで、幅広い作業に不可欠な役割を果たしています。自動車部品の精度と品質向上に貢献しています。
木工産業:
木工職人は、木材の表面を整形し、滑らかにするために研磨ディスクを使用します。これらのディスクは、余分な材料を取り除き、形状を整え、さらなる仕上げのための木材の準備に効果的です。
一般製造業:
研削ディスクは、正確な材料除去が必要なさまざまな製造プロセスに使用され、高品質の部品の製造に貢献します。
C. 共通の課題
ディスクの摩耗と擦り傷:
継続的に使用すると、研削ディスクが摩耗し、性能が低下する可能性があります。効率を維持するには、定期的な点検と交換が必要です。
過熱:
長時間使用中に過度の摩擦が発生すると、ディスクが過熱し、ディスクの耐久性と仕上げ面の品質に影響を及ぼす可能性があります。適切な冷却対策と定期的な休憩が不可欠です。
詰まり:
研磨ディスクには材料の残留物が蓄積し、研磨効果が低下することがあります。定期的な清掃や目詰まり防止機能付きのディスクを選ぶことで、この問題を防ぐことができます。
振動とぐらつき:
バランスの崩れや摩耗の不均一は振動やぐらつきの原因となり、仕上がりの品質と作業の安全性の両方に影響を与える可能性があります。適切な設置とバランス調整は非常に重要です。
ディスクの選択が間違っています:
特定の材質や用途に適さない研削ディスクを選択すると、効率が低下し、損傷につながる可能性があります。材質の適合性に基づいて適切なディスクを選択することが重要です。
研削ディスクの定義、重要性、そして潜在的な課題を理解することは、これらのツールを利用する業界にとって不可欠です。一般的な問題に対処し、適切な使用方法を確保することで、各業界はそれぞれの用途において研削ディスクの有効性を最大限に高めることができます。
研削ディスクの摩耗
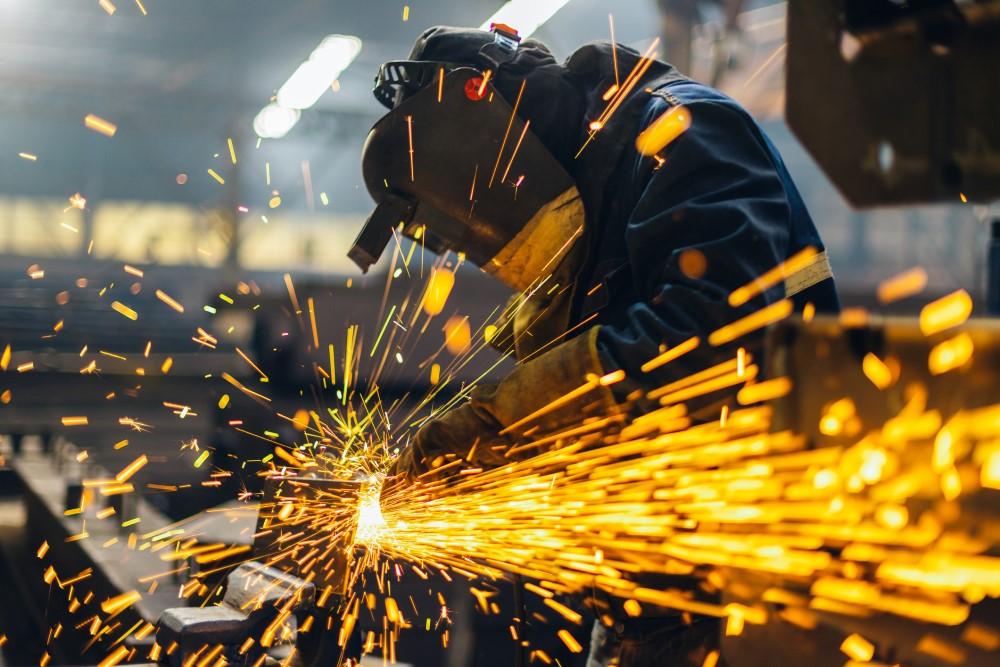
研削ディスクは、金属加工からコンクリート研磨まで、様々な産業において不可欠なツールであり、必要な研磨力を提供します。研削ディスクの摩耗に寄与する要因を理解することは、その性能を最適化し、安全性を確保する上で非常に重要です。
材料の硬度と組成:
硬度の変化:研削ディスクは、硬度の異なる材料に接触します。金属やコンクリートなどの研磨材は、硬度が大きく異なる場合があります。硬い材料を継続的に研削すると、摩耗が加速されます。
素材構成:研削対象物に研磨剤が含まれていると、研削ディスクの摩耗に影響を与える可能性があります。研磨粒子はディスクの摩耗を加速させる可能性があります。
研削圧力と力:
過度の圧力:研削ディスクに過度の圧力をかけると、摩耗が早まる可能性があります。ディスクに不要な負担をかけないように、特定の用途に適した推奨圧力を使用することが重要です。
不十分な力: 一方、力が不十分だと研削時間が長くなり、余分な摩擦と熱が発生して摩耗が促進される可能性があります。
ディスクの品質と構成:
研磨材の品質:研磨ディスクに使用される研磨材の品質は、その寿命に大きく影響します。高品質の研磨材は摩耗に強く、切れ味を長く維持する傾向があります。
接着剤:研磨粒子を結合させる接着剤は重要な役割を果たします。適切に設計された接着剤はディスクの耐久性を高めます。
労働環境条件:
温度:研削中に発生する高温は、ディスクの構成に影響を及ぼす可能性があります。過度の熱は接着剤の強度を弱め、摩耗を加速させます。
湿気と汚染物質:作業環境において湿気や汚染物質にさらされると、研削ディスクの完全性が損なわれ、摩耗が早まる可能性があります。
オペレーターのテクニック:
適切なテクニック:オペレーターのスキルと技術は非常に重要です。不適切な角度で研磨したり、過度の力で研磨したりするなど、不適切な使用方法は、ディスクの摩耗を不均一にし、寿命を縮める可能性があります。
定期検査:作業者は、研削ディスクに損傷や摩耗の兆候がないか定期的に点検する必要があります。一定以上の摩耗が見られるディスクは、速やかに交換してください。
ディスクサイズとRPMの互換性:
正しいサイズ:グラインダーに適したディスクサイズを使用することは非常に重要です。サイズが不適切なディスクは、摩耗が不均一になったり、安全上のリスクが生じたりする可能性があります。
RPM 互換性:研削ディスクの推奨回転数 (RPM) を遵守することで、最適なパフォーマンスが確保され、早期摩耗を防ぐことができます。
定期的なメンテナンス、推奨運転条件の遵守、そして作業に適した研削ディスクの選択は、摩耗を最小限に抑えるために不可欠です。摩耗に影響を与える要因を理解することで、オペレーターは研削ディスクの寿命と効率を向上させ、より安全で生産性の高い研削作業に貢献できます。
不均一な研削
研削ムラとは、研削面が均一で滑らかな仕上がりにならない状態を指します。この問題は様々な原因で発生し、ワークピースの品質に影響を与える可能性があります。ここでは、研削ムラにつながる一般的な要因とその解決策をご紹介します。
研削ホイールの選択が不適切:
解決:研削する材料に適した研削ホイールを選択してください。材料によって研磨特性が異なります。用途に合わせて適切なホイールタイプ、粒度、ボンドを選択してください。
不適切なホイールドレッシング:
原因:研削ホイールが適切に研磨されていないと、摩耗が不均一になり、切断が効果的に行われない可能性があります。
解決:砥石の形状を維持し、蓄積した切削片を除去するために、定期的に砥石をドレッシングしてください。適切なドレッシングを行うことで、均一な切削面が得られます。
研削液または冷却液の不足:
原因:研削液の使用が不十分であったり不適切であったりすると、摩擦と熱が増加し、研削が不均一になる可能性があります。
解決:適切な研削液または冷却剤を使用して熱を放散し、摩擦を軽減します。均一な結果を得るには、適切な冷却が不可欠です。
研削パラメータが正しくありません:
原因:過度の速度、送り速度、または切削深さなどの不適切な研削パラメータを使用すると、研削が不均一になる可能性があります。
解決:材料と用途に応じて研削パラメータを調整してください。最適な設定については、メーカーの推奨事項を参照してください。
摩耗した研削ホイール:
原因:摩耗した研削ホイールでは、均一な切削面が得られず、研削が不均一になる可能性があります。
解決:研削砥石は耐用年数に達したら交換してください。定期的に摩耗の兆候がないか点検してください。
不均一な圧力または供給速度:
原因:研削中に不均一な圧力や一定しない送り速度が発生すると、材料の除去が不規則になる可能性があります。
解決:ワークピース全体に均一な圧力をかけ、一定の送り速度を維持します。オペレーターのスキルと細部への注意が重要です。
マシンの問題:
原因:研削盤の機械的な問題(位置ずれやスピンドルの問題など)により、研削が不均一になる可能性があります。
解決:研削盤の定期的なメンテナンス点検を実施してください。機械的な問題が発生した場合には、速やかに対処し、適切な機能を確保してください。
ワークピース固定具:
原因:ワークピースが適切に固定されていなかったり、位置がずれていると、研削が不均一になる可能性があります。
解決:ワークピースの適切な固定と位置合わせを行ってください。研削工程中にワークピースが動かないようにしっかりと固定してください。
研削ムラに対処するには、適切な機器のセットアップ、正しい運転パラメータ、そして定期的なメンテナンスが必要です。研削アプリケーションにおいて高品質で安定した結果を得るには、オペレーターが問題を迅速に特定し、修正できるよう訓練を受ける必要があります。定期的な点検とベストプラクティスの遵守は、研削プロセスにおける効率的で均一な材料除去に貢献します。
過熱の問題
研削中の過熱は、研削ホイールとワークピースの両方の性能に影響を与える一般的な問題です。過度の熱は、ホイール寿命の短縮、ワークピースへの熱損傷、全体的な研削効率の低下など、さまざまな問題を引き起こす可能性があります。過熱の問題に対処するための潜在的な原因と解決策を以下に示します。
研削パラメータが正しくありません:
原因:過度の速度、送り速度、切削深さなどの不適切な研削パラメータを使用すると、過剰な熱が発生する可能性があります。
解決:推奨範囲内で粉砕パラメータを調整してください。粉砕する材料に応じた最適な設定については、メーカーのガイドラインを参照してください。
冷却または潤滑不足:
原因:冷却剤や研削液の使用が不十分だと、摩擦と熱が増加する可能性があります。
解決:研削工程中は、十分な冷却剤または潤滑剤の供給を確保してください。適切な冷却は熱を放散させ、熱による損傷を防ぎます。
ホイールの選択が間違っています:
原因:研削する材料に対して不適切な仕様の研削ホイールを選択すると、過熱につながる可能性があります。
解決:特定の用途に適した研磨剤の種類、粒度、結合剤を備えた研削ホイールを選択してください。材料に適したホイールを選ぶことで、熱の発生を最小限に抑えることができます。
ワークピース材質の問題:
原因:一部の材料、特に熱伝導率の低い材料は、研削中に過熱しやすくなります。
解決:熱伝導率の低い材料の場合は、研削パラメータを調整してください。熱に弱い材料用に設計された専用の研削砥石の使用を検討してください。
ホイールドレッシングの問題:
原因:研削ホイールの不規則性や不適切なドレッシングは、接触の不均一や熱の蓄積につながる可能性があります。
解決:研削砥石の形状を維持し、目詰まりや堆積した研磨屑を取り除くために、定期的に研磨砥石をドレッシングしてください。適切にドレッシングされた砥石は、安定した研削性能を保証します。
不適切な機械メンテナンス:
原因:研削盤のメンテナンスが不十分だと、過熱の問題が発生する場合があります。
解決:研削盤の定期メンテナンスを実施し、冷却システムの点検、砥石ドレッシング装置の点検、適切なアライメントの確認などを行います。機械的な問題が発生した場合には、速やかに対処してください。
ホイール冷却水流量不足:
原因:研削ゾーンへの冷却剤の流れが不十分だと、熱放散が減少する可能性があります。
解決:クーラント供給システムを点検し、最適化します。冷却効率を維持するために、クーラントが研削ゾーンに効果的に届くようにします。
研削時間が長すぎる場合:
原因:休憩なしで長時間研磨を続けると、熱が蓄積される可能性があります。
解決:過度の熱蓄積を防ぐため、断続的な研削を行い、休憩を挟むようにしてください。このアプローチは、特に大規模な研削作業や難易度の高い研削作業において重要です。
研削における過熱問題に対処するには、適切な機器のセットアップ、適切な研削パラメータ、そして定期的なメンテナンスを含む包括的なアプローチが必要です。オペレーターは、最適な性能、工具寿命の延長、そして高品質な結果を確保するために、研削工程中の熱発生を監視・制御する必要があります。
振動に関する懸念
研削作業中の過度の振動は、表面品質の低下、工具摩耗の増加、研削盤の損傷など、様々な問題を引き起こす可能性があります。振動の問題に対処することは、精密で効率的な研削プロセスを実現するために不可欠です。以下に、振動の問題を軽減するための潜在的な原因と解決策を示します。
ホイールの摩耗の不均一性:
原因:研削ホイールの不規則な摩耗により、ワークピースとの接触が不均一になり、振動が発生する可能性があります。
解決:研削砥石を定期的に点検し、研磨することで、均一で平坦な表面を維持できます。適切な砥石メンテナンスは振動を最小限に抑えるのに役立ちます。
アンバランスな研削ホイール:
原因:研削ホイールの不均衡は、摩耗の不均一性や製造上の欠陥が原因で、振動を引き起こす可能性があります。
解決:ホイールバランサーを使用して、研削砥石のバランスを調整します。バランス調整により、重量が均等に分散され、作業中の振動が軽減されます。
不適切な機械校正:
原因:ホイールスピンドルや作業台などの機械コンポーネントの調整が不十分であったり、位置ずれがあると、振動の原因となることがあります。
解決:機械の正常な動作を確保するため、定期的に機械部品の調整と調整を行ってください。機械のセットアップと調整については、メーカーのガイドラインに従ってください。
ワークピースのアンバランス:
原因:ワークピースが不均一であったり、適切に固定されていない場合は、不均衡が生じ、振動が発生する可能性があります。
解決:ワークピースを適切に固定し、均等な位置とクランプで固定してください。研削工程を開始する前に、アンバランスの問題に対処してください。
ホイールの選択が間違っています:
原因:不適切な仕様の研削砥石を使用すると振動が発生する可能性があります。
解決:研削する材料に適した研磨剤の種類、粒度、結合剤を備えた研削ホイールを選択してください。用途に合わせてホイールを選定することで、振動を最小限に抑えることができます。
機械の消耗:
原因:ベアリングやスピンドルなどの機械部品が摩耗または損傷すると、振動の原因となることがあります。
解決:摩耗した機械部品は定期的に点検し、交換してください。適切なメンテナンスは過度の振動を防ぎ、研削盤の寿命を延ばすのに役立ちます。
冷却水流量不足:
原因:研削ゾーンへの冷却水の流れが不十分だと、熱が蓄積して振動が発生する可能性があります。
解決:適切な冷却を確保するために、冷却剤供給システムを最適化します。効果的な冷却は、振動につながる熱膨張と収縮のリスクを軽減します。
ツールホルダーの問題:
原因:ツールホルダーまたはスピンドルインターフェースに問題があると、振動が発生する可能性があります。
解決:ツールホルダーがしっかりと取り付けられ、スピンドルと正しく位置合わせされていることを確認してください。振動を最小限に抑えるため、高品質で適切にメンテナンスされたツールホルダーを使用してください。
機械の基礎:
原因:機械の基礎が貧弱であったり、サポートが不十分だと、振動が大きくなる可能性があります。
解決:研削盤は、安定した適切な設計の基礎に設置されていることを確認してください。構造上の問題があれば対処し、機械に伝わる振動を最小限に抑えてください。
研削における振動の問題に効果的に対処するには、適切な機械メンテナンス、砥石の選定、そしてワークピースの取り扱いを組み合わせる必要があります。オペレーターは定期的な点検とメンテナンスを実施し、問題を迅速に特定・解決することで、研削性能と品質を向上させることができます。
研削における負荷の問題
研削における目詰まりとは、研削ホイール上の砥粒間の隙間が被研削材料で満たされ、切削力が低下し、摩擦が増加する現象を指します。目詰まりは、研削工程の効率と品質に悪影響を及ぼす可能性があります。目詰まりの問題に対処するための潜在的な原因と解決策を以下に示します。
ソフトワークピース材質:
原因:柔らかい材料を研削すると、研磨粒子がすぐに詰まってしまう可能性があります。
解決:柔らかい材料を加工する場合は、粗い粒度とオープン構造の研削ホイールを使用してください。これにより、急激な目詰まりを防ぎ、効率的な切削片除去が可能になります。
材料汚染:
原因:ワークピース材料に含まれる油、グリース、冷却剤の残留物などの汚染物質が、負荷の原因となることがあります。
解決:研削前にワークピースを適切に洗浄し、汚染物質を除去してください。適切な切削液やクーラントを使用することで、負荷を最小限に抑えることができます。
冷却剤の不適切な塗布:
原因:冷却剤の塗布が不十分または不適切だと、潤滑と冷却が不十分になり、負荷がかかる可能性があります。
解決:クーラントの流量と濃度を最適化します。クーラントが研削ゾーンに効果的に到達し、潤滑と冷却を行い、目詰まりを防ぎます。
ホイールの切れ味が不十分:
原因:鈍くなったり摩耗した研削ホイールは、切削効率が低下するため、目詰まりが発生しやすくなります。
解決:研削砥石の切れ味を維持するには、定期的にドレッシングと研磨を行ってください。砥石ドレッサーを使用すると、新しい砥粒が露出し、切削力が向上します。
低速ホイール:
原因:研削ホイールを低速で操作すると、チップを排出するのに十分な遠心力が得られず、目詰まりが発生する可能性があります。
解決:研削盤が、特定の砥石とワークピースの組み合わせに適した推奨速度で動作していることを確認してください。速度を上げると、切削片の除去効率が向上します。
過度の圧力:
原因:研削中に過度の圧力をかけると、材料がホイールに押し込まれ、目詰まりが発生する可能性があります。
解決:適度で一定の研削圧力をかけてください。送り速度を調整することで、過度の圧力による目詰まりを防ぎ、ホイールが効率的に切削できるようにします。
ホイールの仕様が間違っています:
原因:研削する材料に対して不適切な仕様の研削ホイールを使用すると、負荷がかかる可能性があります。
解決:特定の用途に適した研磨剤の種類、粒度、結合剤を備えた研削ホイールを選択してください。材料に適したホイールを選ぶことで、目詰まりを防ぐことができます。
不十分な冷却剤洗浄:
原因:汚染された冷却剤や古い冷却剤が負荷の問題の原因となる場合があります。
解決:汚染物質の蓄積を防ぐため、定期的に冷却液を洗浄・交換してください。新鮮で清潔な冷却液は潤滑と冷却効果を高め、目詰まりの可能性を低減します。
不適切な着衣方法:
原因:研削ホイールのドレッシングが不適切だと、不規則性や負荷が生じる可能性があります。
解決:適切なドレッシングツールを使用して、ホイールを適切にドレッシングしてください。ホイールのプロファイルが均一で、凹凸がないことを確認し、負荷がかからないようにしてください。
目詰まりの問題に効果的に対処するには、適切な砥石の選定、機械のセットアップ、そしてメンテナンスの実施が不可欠です。オペレーターは推奨手順に従い、適切な研削パラメータを使用し、定期的に砥石ドレッシングを実施することで、目詰まりを最小限に抑え、研削性能を最適化する必要があります。
様々な金属加工・製造工程において最適な結果を得るには、適切な研削ディスクの選択が不可欠です。最適なディスクの選択は、加工対象材料、希望する仕上げ、使用するグラインダーの種類などの要因によって異なります。
適切な研削ディスクの選び方
材料の適合性:
鉄鋼(鋼、鉄):鉄系金属用に特別に設計された研磨ディスクを使用してください。これらのディスクには、鋼の硬度に適した研磨剤が含まれていることが多く、目詰まりしにくいのが特徴です。
非鉄金属(アルミニウム、真鍮):目詰まりを防ぐため、柔らかい金属に適した研磨剤入りのディスクをお選びください。一般的には、酸化アルミニウムや炭化ケイ素製のディスクが選ばれます。
研磨材:
酸化アルミニウム:鉄系金属の汎用研削に適しています。耐久性と汎用性に優れています。
ジルコニアアルミナ:より高い切削効率と長寿命を実現し、鉄金属および非鉄金属の強力な研削に適しています。
シリコンカーバイド:非鉄金属や石材の研磨に最適です。アルミナよりも鋭利ですが、耐久性は劣ります。
粒度:
粗い粒子(24~36)素早い素材除去と強力な研削。
中粒度(40~60)ストック除去と表面仕上げのバランスをとります。
細粒度(80~120)滑らかな仕上がりを実現し、表面処理や軽い研磨に適しています。
ホイールタイプ:
タイプ27(中央陥没):表面が平らな標準研磨ディスク。表面研磨やエッジ作業に最適です。
タイプ29(円錐形):積極的なストック除去とより優れた表面ブレンディングを実現する角度付きデザイン。
タイプ1(ストレート):切断用途に使用します。薄型形状で正確な切断が可能です。
応用:
研削:材料の除去と成形のための標準研削ディスク。
切断:切断ホイールを使用すると、金属を切断して真っ直ぐできれいな切断面を得ることができます。
フラップディスク:研磨と仕上げを1つにまとめました。表面のブレンドや平滑化に最適です。
グラインダーとの互換性:
グラインダーの機種と速度に適合したグラインダーディスクを使用してください。ディスクの最大回転数(RPM)については、メーカーの推奨値をご確認ください。
タスクの特異性:
大量のストックの除去:効率的な材料除去のために、粗い粒子とタイプ 27 またはタイプ 29 のディスクを選択します。
表面仕上げ:より滑らかな仕上がりのために、フラップ ディスク付きの中粒度から細粒度を選択してください。
安全に関する考慮事項:
安全メガネや手袋などの適切な個人用保護具 (PPE) を着用するなど、安全ガイドラインに従ってください。
耐久性と安全性を高めるために強化ディスクを選択してください。
ブランドと品質:
品質と安定性で定評のあるブランドのディスクをお選びください。高品質のディスクは、優れたパフォーマンスと耐久性を提供します。
コストの考慮:
初期費用と、研磨ディスクの期待寿命および性能とのバランスを検討してください。高品質のディスクは初期費用が高くなる場合がありますが、長期的に見てより高い価値を提供します。
これらの要素を考慮することで、オペレーターは特定の用途に適した研削ディスクを選択し、効率、安全性、最適な結果を確保できます。
結論
結論として、適切な研削ディスクの選択は、金属加工および製造工程で成功を収める上で極めて重要な要素です。その選択は、加工対象材料、希望する仕上げ、使用するグラインダーの種類など、様々な要因によって異なります。材料の適合性、研磨剤の種類、粒度、ホイールの種類、用途、グラインダーの適合性、作業の特殊性、安全性、ブランドの品質、そしてコストを考慮することで、オペレーターは研削工程における効率と安全性を向上させるための情報に基づいた意思決定を行うことができます。
安全ガイドラインを遵守し、適切な個人用保護具を着用し、グラインダーとディスクの互換性に関するメーカーの推奨事項に従うことが不可欠です。重切削、表面仕上げ、切断など、用途を問わず、適切な研削ディスクは作業の品質と効率に大きな影響を与えます。
さらに、摩耗や損傷を定期的にチェックし、過熱や振動の問題に対処し、負荷の問題を理解することで、研削ディスクの寿命が延び、一貫したパフォーマンスが確保されます。
要約すると、研削ディスクの選択、使用、保守に対する十分な情報に基づいた体系的なアプローチが、最適な結果の達成、生産性の向上、安全な作業環境の確保の鍵となります。
投稿日時: 2024年1月12日